Tips for Choosing the Right Metal for a Fabrication Project
Metal fabrication is an essential process in various industries, helping companies craft products and structures that look good and withstand the test of time. The choice of metal plays a crucial role in determining success, durability, and cost-effectiveness.
Follow along as we offer expert tips for choosing the right metal for a fabrication project and ensuring success while aligning with your specific requirements and goals.
Why Metal Choice Matters in Fabrication
Selecting the appropriate metal is fundamental to the longevity and performance of the finished product. Different metals offer varying levels of strength, malleability, and resistance to environmental factors such as corrosion and temperature changes.
The metal choice also impacts the fabrication process itself, affecting factors such as weldability, cutting, and forming capabilities. Understanding the specific demands of your project and how different metals can meet those demands will ensure efficiency, reduce costs, and result in a product that meets industry standards for quality and resilience.
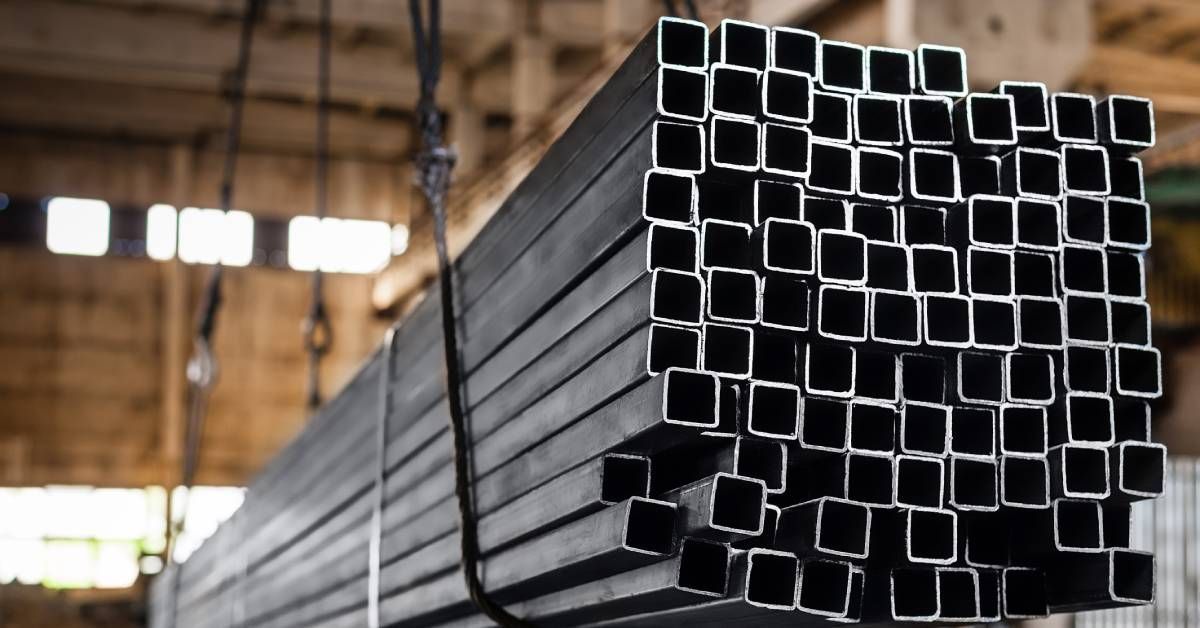
Examples of Fabrication Projects That Require Metal
There are all sorts of modern fabrication processes that use metal as a fundamental component.
Building Construction
Metal is a cornerstone in the building construction industry, and contractors use it for structural elements such as beams and columns, as well as for roofing and cladding materials. The strength and durability of metals such as steel and aluminum make them ideal for supporting large structures and ensuring long-lasting protection against environmental elements.
Automotive Manufacturing
In automotive manufacturing, metals are essential for the production of body panels, engine components, and structural frameworks. Materials such as high-strength steel, aluminum, and titanium can enhance durability, reduce weight, and improve fuel efficiency while adhering to the industry’s stringent safety and performance standards.
Aerospace Applications
The aerospace sector relies heavily on metals due to their strength-to-weight ratio and ability to withstand extreme pressure and temperature changes. Many use aluminum and titanium for aircraft structures, while more specialized alloys are common in turbine engines and other critical components.
Electronics and Electrical Equipment
Metals play a pivotal role in the fabrication of electronics and electrical equipment. Copper’s excellent electrical conductivity makes it indispensable for wiring and connectors, while aluminum is suitable for heat sinks and housing. Using these metals ensures efficient power management and thermal regulation, which is critical for the performance of electronic devices.
Marine and Offshore Structures
For marine and offshore applications, metals such as stainless steel and galvanized steel are preferred due to their corrosion resistance when exposed to saltwater and harsh marine environments. These properties make them suitable for ships, submarines, oil rigs, and other maritime and coastal constructions that demand robust materials.
Medical Devices and Implants
The medical field uses metal for surgical instruments, orthopedic implants, and prosthetics. Titanium stands out due to its biocompatibility, strength, and corrosion resistance, providing long-lasting solutions that integrate well with human tissue while maintaining structural integrity and functionality.
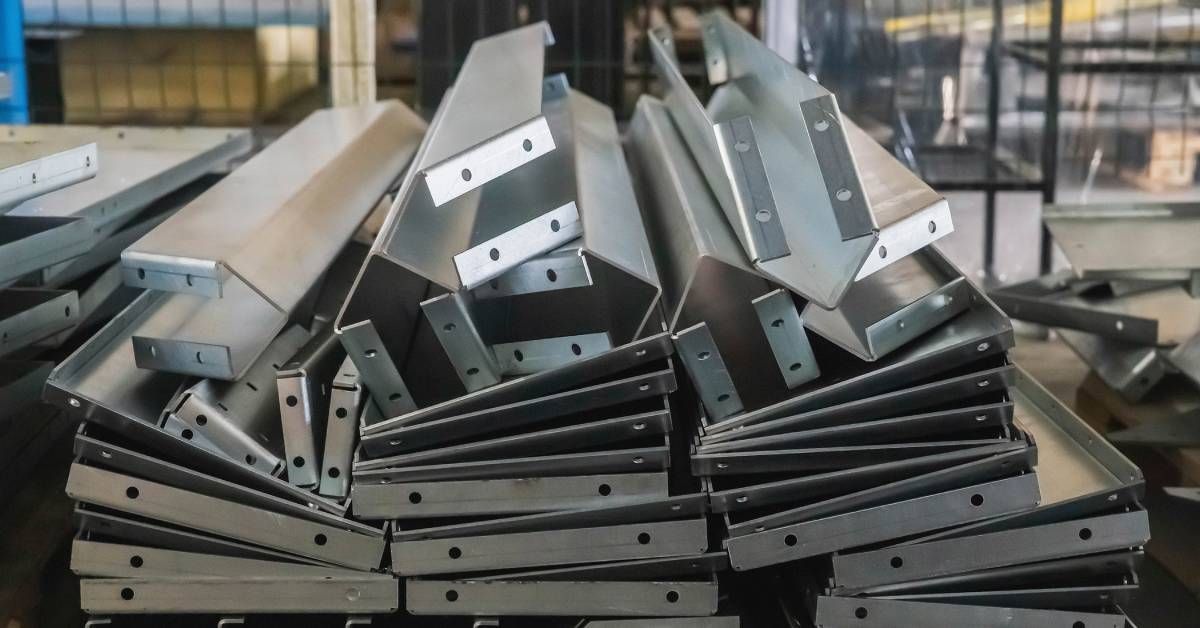
What To Consider When Choosing Metal for Fabrication
If you’re using metal in your fabrication process, there are a few key factors to consider.
Cost Considerations
When planning a fabrication project, cost is a critical factor influencing metal selection. The price of metals can vary significantly based on their composition, availability, and market demand. Common metals like carbon steel are typically more budget-friendly, making them a popular choice for projects with tighter financial constraints. However, specialized metals, such as titanium or alloys designed for specific environmental conditions, may incur higher costs but offer superior performance benefits.
Assessing Material Strength and Weight
When selecting a metal for fabrication, it’s important to consider the material’s strength-to-weight ratio. This ratio is particularly crucial in industries like aerospace and automotive, where reducing weight without sacrificing strength can lead to improved performance and fuel efficiency. Metals such as titanium offer an excellent balance between lightweight properties and high strength, making them desirable for such applications.
Evaluating Corrosion Resistance
Corrosion resistance is another critical factor, especially in environments exposed to moisture, chemicals, or extreme weather conditions. For instance, many favor stainless steel because of its remarkable resistance to rust and corrosion, making it suitable for outdoor and marine applications. Understanding the specific environmental stresses your project will face will guide the choice of metal with the appropriate protective qualities.
Considering Fabrication and Machinability
The ease of fabrication and machinability is vital to efficient project completion. Some metals, like aluminum, are more pliable and easier to machine, which can speed up production times and reduce labor costs. Metals that are difficult to weld or cut may require additional specialized equipment or skilled labor, impacting overall project cost and timeline. Analyze the fabrication requirements of your design to ensure a smooth manufacturing process.
Examining Temperature and Heat Tolerance
Certain projects demand metals that can withstand extreme temperatures or high thermal cycles. For applications that involve high heat, such as engine parts or industrial furnaces, metals like Inconel or tungsten offer the ability to maintain structural integrity under thermal stress. Evaluate the thermal demands of your application to select a metal that will perform reliably under the specified conditions.
Sustainability and Environmental Impact
In today’s environmentally conscious world, sustainability and environmental impact are increasingly important considerations in metal fabrication. Choosing metals that are recyclable and have a lower carbon footprint can significantly contribute to a project’s overall sustainability. Additionally, sourcing metals from suppliers that prioritize sustainable mining practices and energy-efficient processes can further reduce the environmental impact of a fabrication project.
Available Metals and Their Properties
When it comes to metal fabrication, several options are available, each with its strengths, weaknesses, and best applications.
- Stainless steel: Known for its excellent corrosion resistance, durability, and aesthetic appeal, and ideal for applications exposed to moisture and chemicals
- Aluminum: Lightweight with good corrosion resistance, making it ideal for automotive and aerospace applications
- Carbon steel: Strong and cost-effective, suitable for structural applications but requires protective coatings to prevent rust
- Copper: Excellent electrical and thermal conductivity, and often used in electrical wiring and plumbing
- Titanium: Offers a high strength-to-weight ratio and excellent resistance to corrosion and extreme temperatures
- Inconel: Known for its strength and ability to withstand extreme temperatures and thermal cycles, making it ideal for engine components
- Brass: An alloy of copper and zinc known for its malleability, low friction, and acoustic properties, often used in musical instruments and fittings
- Tungsten: Known for its high melting point and strength at elevated temperatures, making it suitable for applications requiring extreme heat resistance
- Galvanized steel: Carbon steel coated with zinc for improved corrosion resistance, commonly used in outdoor and construction projects
By leveraging the expertise and specialized equipment of a professional fabrication company, businesses can benefit from improved product quality and consistency without having to maintain an in-house facility.
Achieving Thoughtful Metal Selection
Choosing the right metal for your fabrication project is a critical decision that impacts the quality of the final product. With these best practices in mind, you can make informed choices that align with your goals. By exploring the ins and outs of the process, you’ll have a clear understanding of the significance of thoughtful metal selection in achieving successful outcomes.
Are you in need of custom metal fabrication services? At H&H Machine Service, we understand the importance of metal selection in the outcome of your projects. See how we can help you get things done faster and more efficiently.
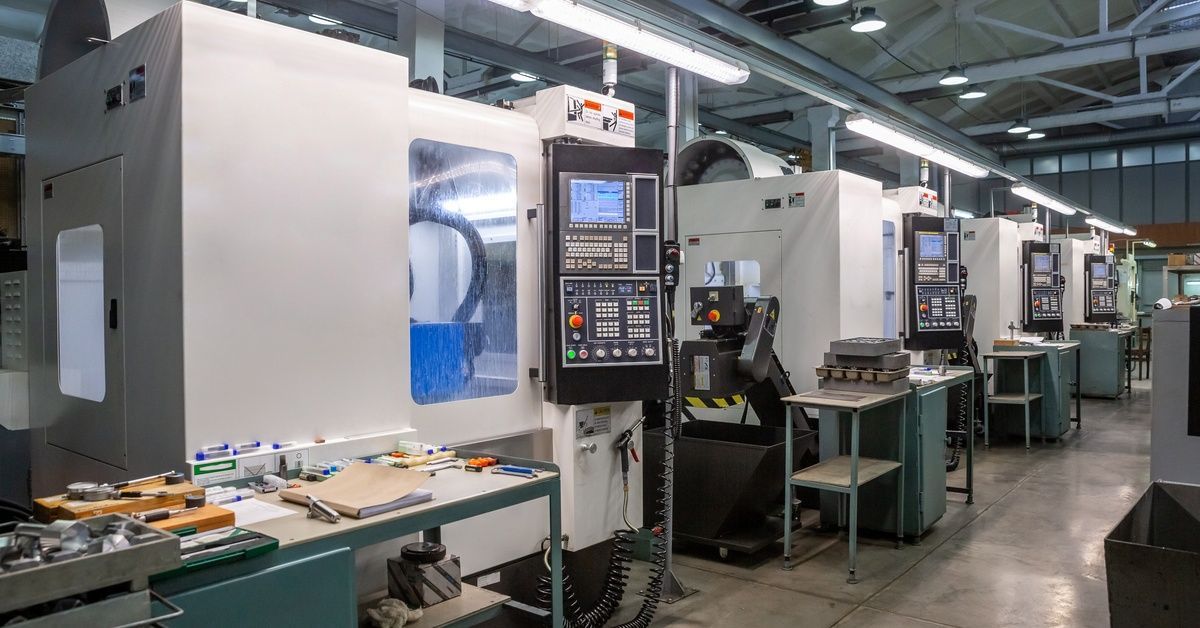